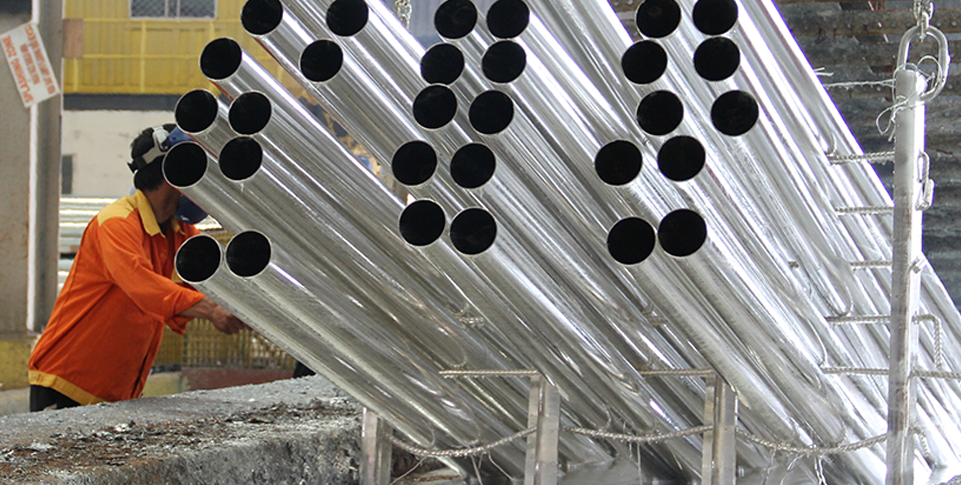

Galvanizing steel products can provide the steel the protection from corrosive reaction when the steel products are getting exposed to open air. The longest Galvanized Tub, with sizes: 14.5 meters (Long), 1.8 meters (Wide) and 2.6 meters (Deep).
Galvanizing will also reduce the total maintenance expenses over the life time of the steel when compared to steel not treated with galvanized process. Characteristics includes: Corrosion resistant (the galvanizing layer prevents rust for decades), Abrasion and impact resistant (zinc alloy layers are harder than base steel) and Cathodic protection (a slightly damaged galvanized layer can still protect exposed steel from corrosion).
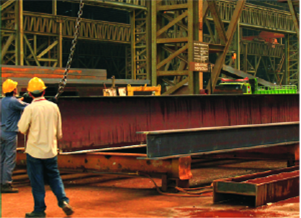
1. PREPARING
This process is the process of preparing and arrangement of the material in a way linked to the positioning aids with slope of 4S degrees.
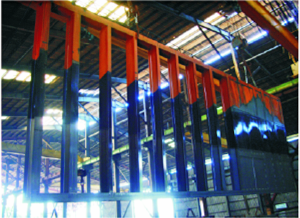
2. DE-GREASING
This process is a process to eliminate oil, oil or grease, varnish and paint Caustic Soda (Na OH) on the use of materials Galvanized be done.
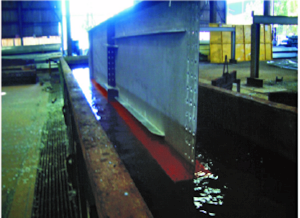
3. WATER RINSING DE-GREASING
This process is process of eliminating residual degreasing fluid.
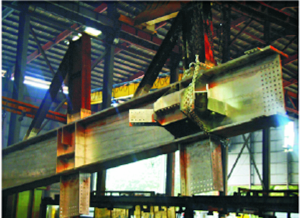
4. PICKLING
This process is a cleaning process to remove rust attached to the material by using Chloride Acid.
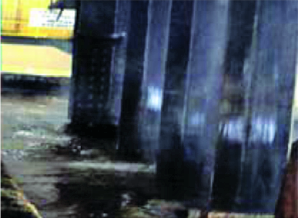
5. DRYING
This is a process to eliminating residual liquids (cleaning of the remaining acid) from the pickling (preservation).
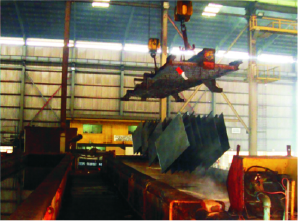
6. PLUXING
This is the process of protect the material from oxidation rust and help the metallurgical Dipping during the process. This process uses Zinc Ammonium Chloride (to the surface).
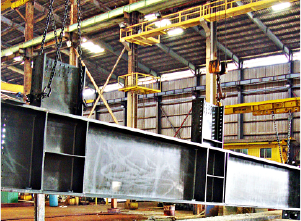
7. DRYING
This process is the process of drying the material so as not to cause explosions and sparks during the process of Dipping.
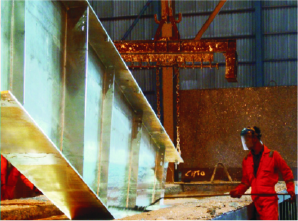
8. DIPPING
This process is the process of dyeing material to Zinc in liquid hot, with temperatures 450-460 Degrees Celsius, so the whole zinc coated materials in metallurgy.
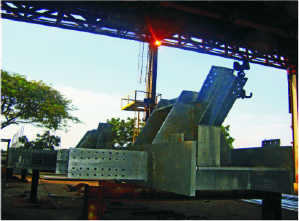
9. COOLING
This process is the cooling material after the Dipping Process.
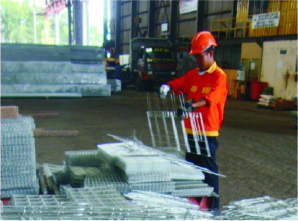
10. FINISHING
This process is a process of arranging material Hot Dip Galvanize process and removing remaining zinc needles.
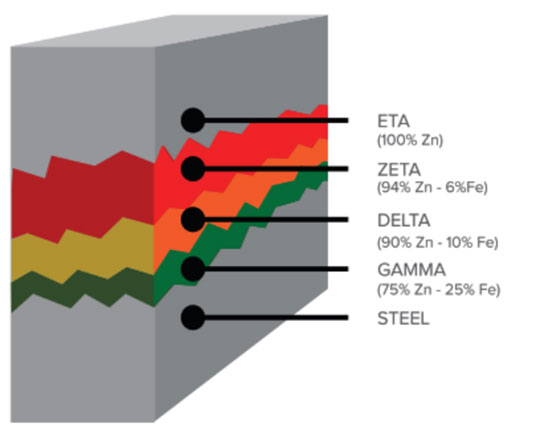
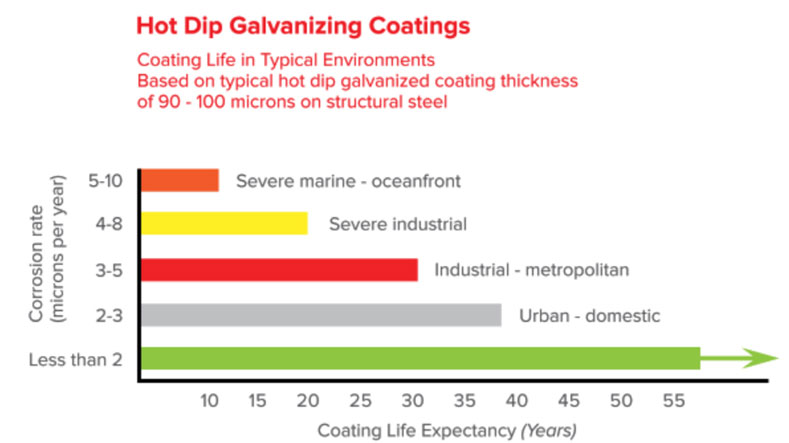